From log to laminated veneer lumber
The use of laminated veneer lumber (LVL) is becoming more popular with designers and architects. Because LVL is created by layering different veneers atop each other, there is a wide variety of process combinations to choose from, but with each combination the structural qualities of the overall LVL varies. It is crucial for manufacturers to know if their available wood will produce LVL that satisfies their customer’s needs. Now, with a new software tool developed by Scion, LVL manufacturers can gauge whether their LVL will likely meet a customer’s performance requirements, without the need to conduct expensive mill tests.
“JNL can see the benefit of this tool to model potential structural finished product output yields...” - Brendan Smith, Technical Services – Product Manager, JNL Group
One of the most important design properties of LVL is bending stiffness. To test the full range of LVL properties, manufacturers have had to process logs and create an LVL sample to check its performance. However, this approach can be expensive and is not always practical in a production setting when trying to assess a wide range of veneers and LVL process options.
Scion was engaged via the Specialty Wood Products Partnership to create a computer model that can determine the bending stiffness range from individual veneers and use that information to calculate the overall LVL section stiffness. It is used as a guide to assist decision making on the likelihood that a forest/log/veneer could meet customer performance requirements and determine what the LVL manufacturing process implications might be.
The computer decision model uses information uploaded about the individual veneer stiffness properties or log pith to bark stiffness profiles and the customer performance/purchase requirements. The user can then explore different LVL process options, and the manufacturer can efficiently use the wood available to them while meeting their customer’s needs.
Brendan Smith Technical Services – Product Manager for the JNL group says, “JNL can see the benefit of this tool to model potential structural finished product output yields, and in being able to determine the required input product mix from two or more distinct log fibre resources. This would enable an increased surety of supply of the required structural grade for the manufacturer’s market, with less potential for arising non-targeted lower grades.”
This software model will save time and money by eliminating unsuitable veneers early in the process. If the model shows that the tested LVL would perform within requirements, then detailed mill studies would be carried out.
As with any model, it is only as good as the input data. The next step to develop the model is to generate and upload more stiffness data for a range of forest/log/veneers.
Investment: Specialty Wood Products Partnership
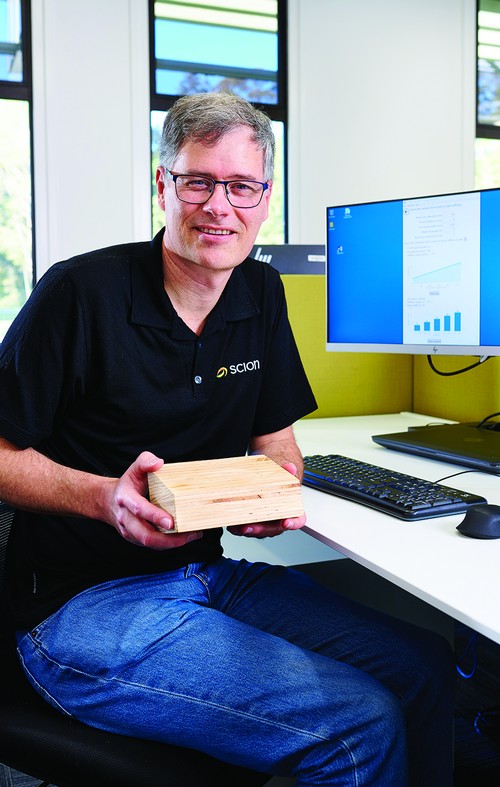