Collaboration creates highly specified filters
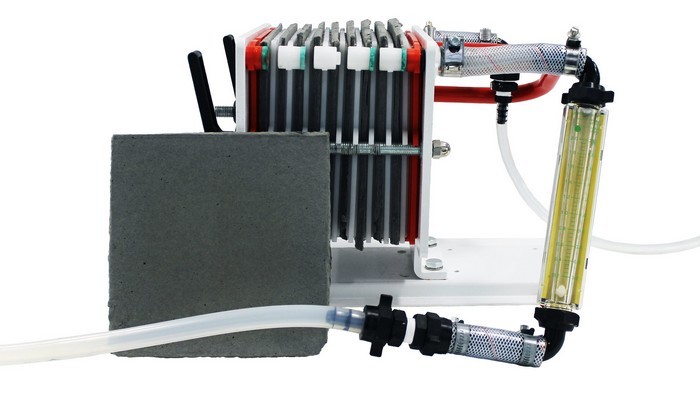
Ligar – a leader in molecular extraction technology and Scion have combined their expertise to create food grade filters so precise they can capture specific molecules.
The collaboration has seen Scion’s pulp and paper engineering expertise united with Ligar’s experience in molecular extraction to produce the paper-based filter embedded with molecularly imprinted polymers known as MIPs.
MIPs
A MIP is a polymer material with a unique impression in it, like a footprint left in the sand which only fits a chosen molecule and can also recognise it from the way the molecule behaves, e.g. charge. MIP technology has been around for some time and is well proven.
The ability to selectively capture and filter material at molecular scale is very useful in concentrating, refining and purifying processes. MIPs can be used to recover highly desirable molecules (valuable metals, for example) for sale or re-processing, and in extracting molecules that are not wanted in the final product (e.g. removing unwanted flavour producing compounds in wine).
There are many industries that can and do make use of such high specialised functionality. However, the integration of the MIPs into the paper-based filter has enabled new applications because of its efficient and functional design.
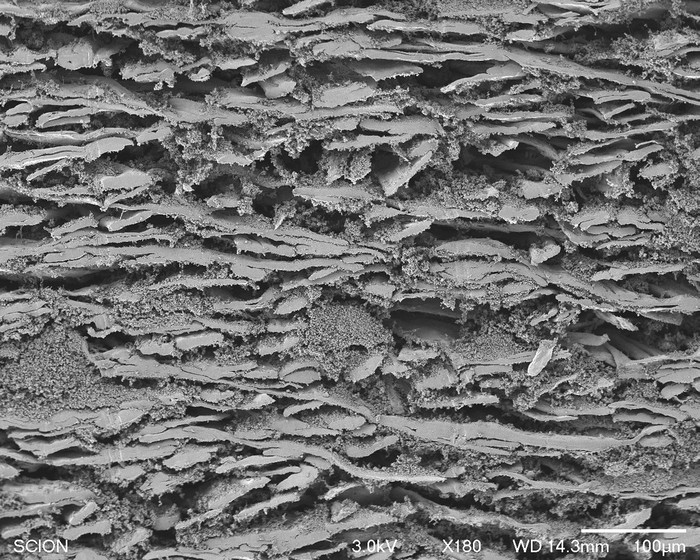
Paper-based solution
MIPs traditionally come in powder form and are mixed into the material to complete the desired recovery/extraction and must then be filtered out. Incorporating MIPs into a paper-based filter designed by Scion scientists, combines the removal and filtration steps into one efficient process.
The fibres in the paper-based filters hold the polymer in place allowing them to work efficiently. Importantly, the fibres in the plates do not capture anything in the filtration process, ensuring the filters can continue to be used in highly selective applications, including food contact applications.
Naturally aligned for biorefining
Beyond the success of the filter plates there is potential for Scion and Ligar to benefit from working together especially in biorefining. The biorefinery concept is comparable to today’s petroleum refineries, which produce multiple fuels and products from petroleum. A biorefinery uses renewable biomass feedstock to be transformed into fuels, power and value-added chemicals. One of the biggest challenges of biorefinery processes is separation and purification of the products. Usually a suite of technologies are used to obtain the purified products – and MIPs could play a key role here.
Scion has long been involved in developing biorefinery processes and there are many applications for Ligar’s established industrial scale separation technology. One example is in the potential for MIPs to pre-concentrate processed biomass, a step that could decrease processing volumes and reduce costs and increase the economic viability for some processes.
Scion’s General Manger for Forests to Biobased Products Dr Florian Graichen says, “We are excited to work with an innovative partner like Ligar on a strategically important part of our 2030 journey – establishing advanced biorefining in New Zealand. Partnerships are critical for us to achieve our big impact aspirations for New Zealand and biorefineries will form an important part of this strategy, moving towards a circular bioeconomy while meeting the Government’s goals for an environmentally and economically susainable future New Zealand”.
The impact of a successful biorefinery network in New Zealand is enormous. Scion’s work in the MBIE-funded bark biorefinery project estimates that the high-value materials created could earn between $400-600 million per annum, contribute $1.8 billion to New Zealand’s GDP and add several thousand new jobs by 2050. Bringing Ligar and Scion’s mutually beneficial technology together will be critical in turning these possibilities into reality.