Green exemplar products pave way for a sustainable future
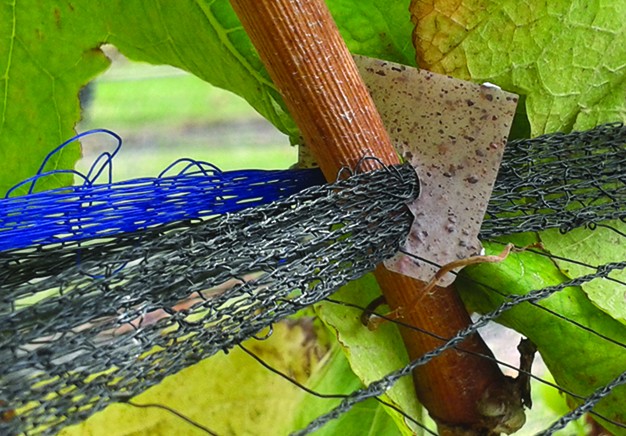
Across the planet the shift from a linear, fossil-fuel based economy to a circular biobased economy is accelerating. Consumers and regulatory bodies are looking beyond price and quality – they are also seeking better environmental standards from products. Through the Scion-led landmark Extrusion Plus research programme, a technology platform has formed to create products that have replaced fossil fuel-based components with renewable natural materials.
The technology takes biomass fillers, such as sander dust, kiwifruit hair and skin, seashells, grape marc, bark or casein and combines them with biobased polymers. Compounding the filler with the polymer creates a biocomposite which is then extruded or reshaped into a new form that can be used in other manufacturing equipment, such as injection moulding.
A big advantage of the technology is its versatility. Product examples include biodegradable vine net clips for the wine industry using grape marc (winemaking waste) composite, a biodegradable utensil for Zespri utilising kiwifruit skin, and a wood compound for a fully biobased and compostable 3D printer filament, now sold by Imagin Plastics.
Considerable effort has also gone into engaging with manufacturing companies. Out of their work has emerged an industry now interested in a shift to using biomaterials.
Described as being ahead of its time, the research generated in this programme has created an important legacy that will continue to help New Zealand transition to a circular bioeconomy.
“Scion is an excellent partner for the plastics industry. The quality of their work was highlighted by their having two finalists in the recent NZ Plastics Industry Design Awards, and gaining a highly commended accolade in the Best Supplier Partnership category. Scion plays an important role in the future of plastics in New Zealand and we look forward to collaborating further on the New Plastics Economy Roadmap project.” - Rachel Barker, CEO, Plastics NZ
Work in the Extrusion Plus programme has gone on to develop capability and infrastructure that will continue to benefit the manufacturing sector. The team has
- set up internationally significant state of the art equipment, facilities and services for the initial processing of small amounts of biopolymers;
- developed technologies for incorporating renewable and locally-sourced biomaterials into polymer composites; and
- can model extrusion parameters for fast optimisation of the overall process.
Other science programmes have also benefitted from the knowledge generated through Extrusion Plus, including
- Scion’s 3D and now 4D printing capability;
- the development of both 3D printing feedstocks that incorporate biomass with bioplastics; and
- printing methods that can handle the variation that comes with using sustainable and renewable resources.
Scion’s WoodforceTM product has also profited from the programme’s investment in twin-screw extrusion modelling software.
Scion’s platform around distributed and modular manufacturing can also be attributed to the Extrusion Plus programme. Distributed manufacturing breaks up the manufacturing process, so that different stages of production can take place in different areas. It is a direct contrast to standard, centralised manufacturing, which requires resources and materials to be transported to a central location where the processing takes place.
If New Zealand were to adopt a distributed manufacturing model for biobased products, for example, we could grow our own high-value bioproduct manufacturing sector in regions with forestry resources and create new uses from side streams like forestry residues.
The Extrusion Plus programme concluded in 2018 after seven years of work. It has laid a foundation and from it, new exemplar products have emerged. We have seen interest and engagement with companies throughout the plastic materials value chain grow and now expect more biobased materials to be used in their products. This includes companies from horticultural, agricultural equipment suppliers, cosmetic industries, through to packaging manufacturers and plastic processors.
Over the course of the programme, presentations have been regularly made at the Plastics NZ annual conference with an obvious growing interest and engagement. Likewise, Scion input at the Board level of Packaging NZ is helping frame the environment for a biomaterials shift.
Although the materials and capability developed at Scion have not yet resulted in a quantum change in plastics usage, the indications show we are on the verge of something significant.