Distributed manufacturing
Mini factories that use residues from production forests, or horticultural, crop and natural fibres to create new wood products, biochemicals and biomaterials.
New technology is making it possible to create mini manufacturing facilities that use a range of biomaterial, including forestry slash, to make wood-products, biofuels and chemicals. These mini factories will enable the transition away from fossil fuels, while supporting economic, environmental and social benefits for our regions. Their success depends on the manufacturing process matched to the available feedstock and creating products that customers demand.
A networked biomass processing sector distributed across New Zealand is well positioned to take advantage of regional opportunities.
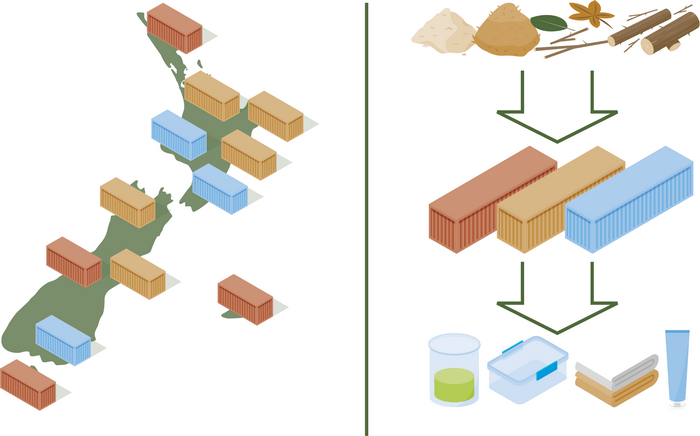
Right process
Distributed manufacturing can play a large role in the forest- based value chain. This process means that mini factories are tailored to process biomass such as forest wood waste, horticultural and farm shelterbelt thinnings or crop residues into high-value wood-based products, biochemicals, or their intermediates.
This is lean, agile, customer-specific manufacturing.
In New Zealand’s current wood processing model, wood is pre-processed at super-skid sites and transported to centralised pulp and paper or timber mills, or it is exported.
In the future, distributed manufacturing will mean that mini factories are tailored to process this woody waste, as well as horticultural or crop residues close to their origin.
Imagine a factory that fits in a shipping container – compact and mobile. These mini factories can be strategically positioned within a forest, orchard or farm where the waste is created. These factories can perform novel scalable processes such as biochemical conversion, pyrolysis and pulping. The choice of process depends on inputs and the product being made.
Around 4 million tons of residue remains in our forests each year. Mobile, tailored mini factories will be key to using this resource.
New Zealand currently exports over 60% of harvested wood as logs for other countries to process and add value. A network of small-scale wood processing units could create value from these logs with the economic, social and environmental benefits of a forest-based bioeconomy returning to the communities in our regions.
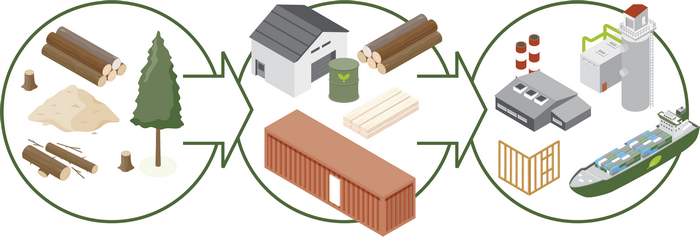
Right region
A biomass processing sector distributed across New Zealand is well positioned to take advantage of regional opportunities. For example, forestry thinnings in Northland, crop stubble from Canterbury and pruned orchard shelterbelts in Hawke’s Bay. Greater processing, making better use of forestry residues, creates high value products, supports regional communities and leads to new employment. Jobs created in manufacturing and engineering in New Zealand tend to create additional employment in support jobs. Similarly, revenue created in manufacturing has a multiplier effect in regional economies, with economic benefits accruing to transport, primary production and commercial construction.
Due to New Zealand’s rugged and often remote forest plantations, transport is an important factor in business decisions and competitiveness. Supporting the value chain with new products that can be delivered in a timely, cost-effective manner is an important part of developing business within the industry.
While New Zealand is fortunate to have plentiful woody biomass feedstocks, they are clumped at landing sites, skid sites and within forests. Lowering the extraction and transport costs of harvesting residues will be key to increasing their use.
Establishing new large central biorefinery infrastructure capable of converting feedstock to biochemicals and bioproducts needs large capital investment. However, mini factories in a distributed network have lower capital required for their establishment and are complementary to new biorefineries. They can be added alongside existing infrastructure. Mini factories create processing options that can generate multiple products from different feedstocks across the forestry, horticultural and cropping sectors.
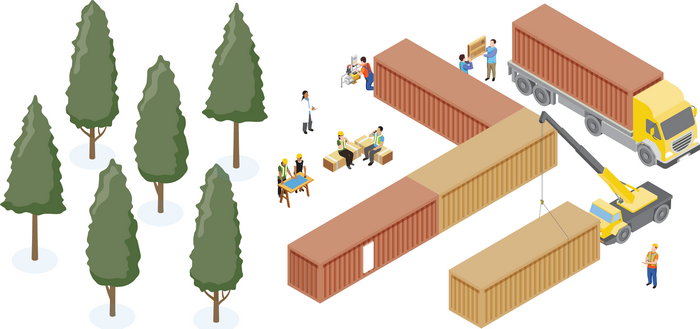
Right product
Responding to the consumer end of the value chain, unique products can be created from biomaterials combining advanced technology, product design and branding.
Distributed manufacturing provides the opportunity to create next-generation bioproducts from forests (and other sources), such as novel wood products, bioplastics, nutraceuticals or pharmaceuticals.
The range of end product opportunities is in the hundreds of thousands, and response to customer demand can be made quickly, not in months or years. Biochemicals synthesised from trees are a new economic activity for New Zealand, making forestry waste streams a valuable commodity.
An example is a liquid intermediate which contains a high proportion of 5-hydroxymethylfurfural (5-HMF) that can be converted to biopolymers and used to create bioplastics.
Mini factories that regionally produce specialised wood products or other biomaterials allow retention of regional identity in those products.
To make this effective, distributed manufacturing plants will be part of a connected industrial ecosystem that ensures that residues and wastes are utilised at their highest value.
The aim is to move New Zealand away from the petroleum-based raw material import model towards a circular forest-based bioeconomy.
The global biochemical market size was estimated at USD 80.81 billion in 2022 and is projected to hit around USD 148.6 billion by 2030.
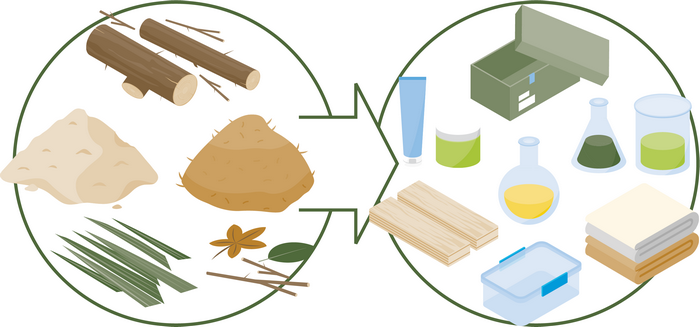
Supporting programmes at Scion
Accelerating and contributing to thriving regions through de-centralised, distributed and circular manufacturing is our focus.
Scion’s distributed biomass conversion programme includes the development of small-scale and modular biorefining processes, collaborating with regional partners to co-develop opportunities in new value chains and markets. We design holistic value-flow systems for regional communities.
The eco-industrial regions programme develops a future fusion of land-use and distributed production systems. It describes intricate ‘value’ webs that accelerate the formation of a human wellbeing centred bioeconomy.
In the modular and circular manufacturing programme, we develop and implement small-scale and modular circular technologies that enable bioproduct manufacturing. It establishes symbiosis driven supply-chain models and manufacturing pathways for forestry and biobased communities.
Where it’s being done
Consumers are increasingly expecting manufacturers to switch from fossil fuel-based resources to renewable bio-based resources, and to adopt circular economy principles where materials are used and reused efficiently.
These drivers lend themselves to a new decentralised model for bioproduct manufacturing in New Zealand and Scion is leading the charge. Our work with new technologies, processes and biobased materials will help to realise our bold vision to increase 10-fold the GDP from forests and manufacturing by 2050.
Here’s some examples of how other companies around the world are making processing equipment mobile to create high-value resources.
Mobile FLIP Project. Forest and agricultural biomass
The Finnish Mobile FLIP (Flexible Industrial Processing of Biomass) project aims to develop mobile manufacturing for agricultural and forest-based biomass resources into products and intermediates. The process is designed to be flexible in terms of raw materials used, as the biomass resources are typically scattered and seasonal. The key technologies used are pelletising, torrefaction, slow pyrolysis, hydrothermal pre-treatment and carbonisation.
The products vary depending on the process concept, being typically fuels (torrefied pellets, biocoals), biochars for soil remediation, biodegradable pesticides, chemicals for the wood panel industry and sugars. Some of the products are intermediates to be further processed by large biorefineries – for which the mobile unit extracts the valuable components or densifies the biomass to reduce transportation costs. mobileflip.eu
Biorefinery Glas. Grass
Biorefinery Glas has small-scale mobile biorefineries on farms in Ireland. The Glas biorefinery converts freshly harvested grass into cattle feed fibre, a protein concentrate feed for monogastrics, a high-value sugar stream of fructo-oligosaccharides and a grass whey for fertiliser or bioenergy applications. The project targets a 40% increase in usable protein per hectare. biorefineryglas.eu
Biofabrik Bio-Refinery. Pasture grass
The first de-centralised biorefinery in the world launched in 2014 in Germany. The Biofabrik Bio-Refinery extracts amino acids from pasture to create vegetable protein, animal feed, fertiliser, cosmetics and pharma products. It uses the existing infrastructure and resources of grass-processing industries to reduce production costs. biofabrik.com/biorefinery
NettEnergy – mobile pyrolysis. Wood, grass, crop residues
NettEnergy in the Netherlands develops and implements scalable pyrolysis technology to convert biomass into materials, chemicals and energy. Examples of conversion include: biochar, pyrolysis oil, wood vinegar and synthesis gas. nettenergy.com
Get in touch
Interested in finding out more about how distributed manufacturing could happen with your business in your region? Scion can bring its domestic and international networks and scientific and process knowledge to future partnerships. Please get in touch to have an initial conversation – we are happy to answer any questions you may have.
Contact
Marc Gaugler, Portfolio Leader, Distributed and Circular Manufacturing